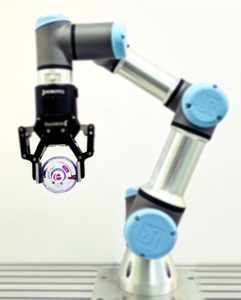
Autonomous Manufacturing for the Innovative enFuse On-Body Infusor
Beyond Smart Manufacturing for the New Generation of User-Administered Infusion Technology
For many years, patients have benefitted from receiving therapeutics via intravenous infusion (IV) at healthcare facilities worldwide. IV-administered medicines have opened doors to new treatments for diseases ranging from oncology to rheumatoid arthritis to migraine to pediatric diseases, and patients have benefited over other prior treatment methods. As formulation technology has evolved and improved, drug delivery device technology has innovated in effort to meet the needs of patients. One such improvement in drug delivery technology is developed and manufactured by Enable Injections—the enFuse® On-Body Infusor.
The enFuse is designed to enable user-administration of therapeutics outside of a healthcare facility. The high-tech enFuse devices are designed, developed, and manufactured in Cincinnati, Ohio.
This Enable blog aims to share the latest thought leadership related to Enable’s advancements and the latest with the enFuse. This month’s content is focused on the mechanics behind the enFuse mechanical delivery device – Enable’s Manufacturing.
Enable Injections and Autonomous Manufacturing
When you hear the word Autonomous, your mind may switch to thoughts about today’s automobiles and developments with self-driving cars. Many cars today have advanced safety features that utilize sensors to detect possible incidents before they happen. The sensors apply decision-making into the safety features of the car, and can assist with decisions, sometimes even before the driver is aware.
Other cars go beyond this and use sensors for more than safety. These advanced cars are truly autonomous in nature and take full control of all decisions, so the driver can sit back and relax. In an autonomous car, a driver can arrive at the destination without making any driving decisions along the way.
Like the autonomous evolution of automobiles, manufacturing is becoming more autonomous. With the advent of Industry 4.0 and the interconnectivity of machines and equipment to our digital lives, data-based decision-making is becoming the reality in many advanced manufacturing sites.
By analyzing data captured by equipment, engineers can implement processes which lead to improved efficiency and reduced costs. But often the timeliness of the decisions and the manual nature of the analysis can cause delays or errors in implementation. In analyzing large amounts of data, the notable events and other reference points may lead manufacturers to only deconstruct adverse events in the manufacturing process. The value of real time data analytics of a large data set requires a new approach to manufacturing.
Smart manufacturing + Industry 4.0 + Pharma 4.0 = e4.0
Enable’s approach to Smart Manufacturing is comprised of a strategic initiative we have labeled e4.0. The objective of e4.0 is to increase manufacturing efficiency through the integration and early adoption of Industry and Pharma 4.0 technologies. Because Enable Injections is a young company, there are no legacy systems to update or change. This allows manufacturing processes and systems to be designed from the ground up using Industry 4.0 technologies.
Pharma 4.0 is a “holistic operating model for pharmaceutical factories and supply chains of the future based on Industry 4.0 capabilities, digital maturity, and data integrity by design.”[i] As pharmaceutical companies are the customer of Enable Injections, and there are many crossover applications to the medical device industry, it makes sense for Enable’s e4.0 strategy to align with the same strategies as Pharma 4.0.
The main two enabling strategies of Pharma 4.0 are digital maturity and data integrity by design. e4.0 details a digital maturity growth strategy as Enable moves from startup into commercial phase. e4.0 also utilizes a proprietary data collection and analysis system we have labeled eNET (Enable network) that is built from the ground up to meet data integrity industry best practices such as ALCOA+.
Modular Scalable Manufacturing – Enable’s approach to meet the customer’s needs
Traditional auto-injectors have had limited verification because they are filled with drug product during manufacturing. The enFuse product is manufactured without the intended drug. While the enFuse is a single-use disposable device from the patient’s perspective, the enFuse was designed to be tested multiple times during manufacturing. These two design features (no pre-filled drug and reusable during manufacturing) allow the process to be highly verified via automated inspection and in-line testing. This ensures a level of quality heretofore unachievable in this market space.
Precision assembly is also required and with the Increased use of robotics from the collaborative lab/development type to full-scale manufacturing with vision-guided 6-axis robots, precise assembly requiring anthropomorphic movements with decision-making capabilities are now achievable on a repeatable basis.
Intelligent real-time automated data analytics
eNET, built from the ground up with digital maturity and data integrity in mind[ii], will serve as both a central data collection system, a human machine interface to control equipment, and analytics and reporting system. eNET is intended to serve multiple customers across both internal and external value chains. For example, the process control and in-line testing information will be correlated to incoming quality control data for components and outgoing quality control data for product performance testing. The enFuse will be covertly serialized to identify trends across the product lifecycle (manufacturing through patient use). Product learning will be fed back to the Engineering teams for product improvements to increase efficiency and reliability.
The strategy of a highly verified process for Continual Process Verification is supplemented by an equally robust data collection and analysis system via eNET. By capturing this data, both data-driven and closed-loop process control processes, as well as automated inspection systems such as camera-based vision systems, can be intelligently programmed to make critical decisions throughout the manufacturing process.
With eNET collecting data from every aspect of the manufacturing process, decisions to move from a Preventive Maintenance (PrevM) to a Predictive Maintenance (PredM) model become much easier and can save not only costly repair to equipment but also save on unnecessary downtime during maintenance windows. The application of eNET will help to meet product quality requirements as well as reduce manufacturing downtime and improve cost, quality, and competitiveness.
Conclusion
The enFuse product technology is both novel and state-of-the-art, bringing tremendous value to patients. Enable Injections e4.0 manufacturing strategy aims to similarly utilize state-of-the-art manufacturing technologies in the enFuse manufacturing process to ensure the highest levels of quality and efficiency, aligning with our mission of being technology experts focused on an exceptional patient experience in collaboration with our biopharma partners.
To learn more about Enable’s enFuse On-Body Infusor and its innovative manufacturing processes, contact us.
Authors:
Andrew Thomas, PhD, Enable Injections, Senior Director, Manufacturing
Brian Costigan, Enable Injections, Manufacturing Engineering Manager
[i] “Pharma 4.0 Hype or Reality”, Pharmaceutical Engineering, July-August 2018, pgs 40-44
[ii] Data Integrity in the Trenches, A Look in the QC Laboratory, Powers & Newhouse, Pharmaceutical Engineering January/February 2019